An electric generator is a device that converts mechanical energy into electrical energy. It is commonly used as a backup power source in case of power outages or in areas where there is no access to the power grid. However, electric generators produce a considerable amount of heat during operation, which can cause damage if not properly dissipated.
This is why proper air circulation is crucial to the efficient and safe operation of electric generators. In this outline, we will discuss the importance of proper air circulation in electric generators, the components of a proper air circulation system, and the maintenance and troubleshooting of air circulation problems.
Explanation Of Electric Generators And Their Functions
An electric generator is a machine that converts mechanical energy into electrical energy. It works on the principle of electromagnetic induction, where a magnetic field is created by the rotation of a coil of wire around a magnet, inducing an electrical current in the wire.
The mechanical energy required for this process can be supplied by various sources such as steam turbines, wind turbines, or internal combustion engines. Electric generators are widely used in various applications, such as powering homes, businesses, and industries, as well as in portable devices such as RVs and boats. They are also used as backup power sources in case of power outages or in areas without access to the power grid.
Importance Of Proper Air Circulation
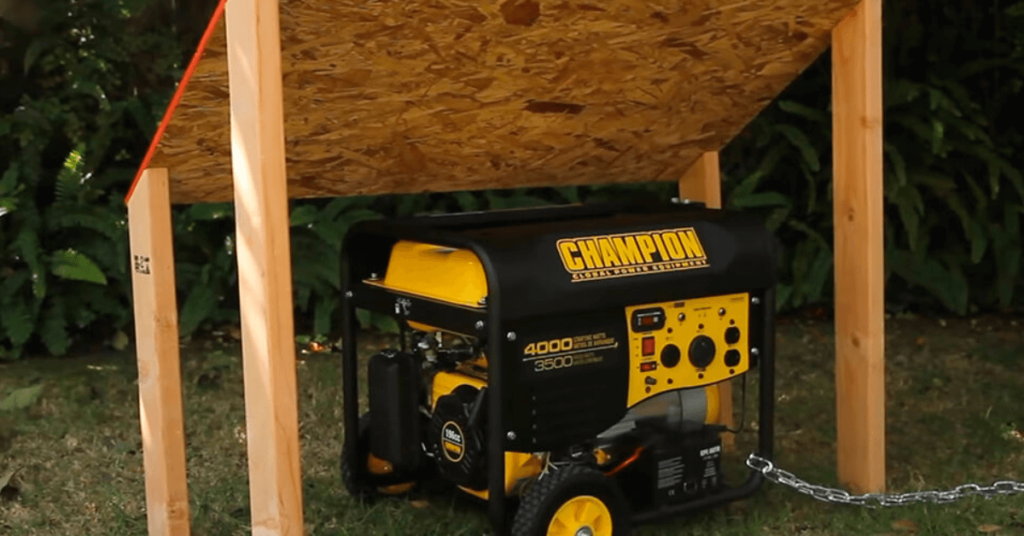
Electric generators produce a significant amount of heat during operation, which can cause damage if not properly dissipated. The importance of proper air circulation in electric generators lies in its ability to efficiently dissipate this heat. The cooling system of an electric generator helps to maintain a safe operating temperature, prevent overheating, and increase the lifespan of the generator. Inadequate air circulation can lead to overheating, which can cause insulation breakdown, reduced efficiency, and even permanent damage to the generator. Therefore, proper air circulation is crucial for the efficient and safe operation of electric generators.
Explanation Of How Electric Generators Produce Heat
Electric generators produce heat during operation due to the conversion of mechanical energy into electrical energy. The process of converting mechanical energy into electrical energy involves the movement of wires and magnets, which generates friction and resistance, causing heat to be produced.
Additionally, the internal combustion engines used to power electric generators produce a considerable amount of heat during operation, which is transferred to the generator. The heat produced during operation must be dissipated to maintain a safe operating temperature and prevent damage to the generator.
Heat Dissipation And The Role Of Air Circulation
Heat dissipation is a critical process in electric generators as excessive heat can cause damage to the generator. Air circulation plays a vital role in heat dissipation in electric generators. The cooling system of the generator helps to remove the heat generated during operation and maintain a safe operating temperature.
The air-cooled or liquid-cooled system of the generator is responsible for circulating air or liquid to dissipate the heat produced by the generator. Air circulation in the generator works by drawing in cool air through the generator’s ventilation system and forcing it over the generator’s components, such as the stator and rotor.
This helps to remove the heat from the generator’s components and transfer it to the surrounding environment. Proper air circulation ensures that the generator’s cooling system functions efficiently, preventing the generator from overheating and sustaining damage.
Effects Of Inadequate Air Circulation On Electric Generators
Inadequate air circulation in electric generators can have severe consequences on the generator’s performance and lifespan. Insufficient airflow can cause the generator to overheat, leading to insulation breakdown and reduced efficiency.
The high operating temperature can also cause the generator’s components to expand and warp, leading to misalignment and damage. This can result in costly repairs or even the need for a complete replacement of the generator.
In addition, inadequate air circulation can cause the generator’s internal parts to accumulate dust and debris, further reducing the efficiency of the cooling system and increasing the risk of damage to the generator. Therefore, proper air circulation is crucial to ensure the efficient and safe operation of electric generators.
Components Of Proper Air Circulation
Proper air circulation in electric generators requires the use of an efficient cooling system. The cooling system comprises several components that work together to circulate air or liquid and dissipate heat from the generator. The components of a proper air circulation system in electric generators include:
- Radiator or heat exchanger: The radiator or heat exchanger is responsible for exchanging the heat absorbed from the generator to the surrounding environment. It is located at the back of the generator and consists of a series of fins that increase the surface area for better heat dissipation.
- Fan: The fan helps to draw cool air through the ventilation system of the generator and force it over the generator’s components, such as the stator and rotor. It is responsible for maintaining a steady flow of air to ensure efficient heat dissipation.
- Air ducts: The air ducts are responsible for directing the flow of air through the generator’s ventilation system. They ensure that the cool air is delivered to the areas where it is needed the most, such as the stator and rotor.
- Coolant: In liquid-cooled generators, the coolant is responsible for absorbing heat from the generator and transferring it to the radiator or heat exchanger. The coolant circulates through the engine block and radiator to remove heat from the generator.
- Pump: The pump in liquid-cooled generators helps to circulate the coolant through the engine block and radiator. It ensures a consistent flow of coolant to maintain an optimum operating temperature.
- Filters: The air and oil filters are responsible for removing debris and contaminants from the air and oil that circulate through the generator. They help to maintain the efficiency of the cooling system and prevent damage to the generator’s components.
- Proper maintenance and regular inspection of these components are crucial to ensure the efficient and safe operation of electric generators.
Cooling Systems And Their Functions
Cooling systems are an essential component of electric generators that help to dissipate heat and maintain safe operating temperatures. There are two main types of cooling systems used in electric generators: air-cooled and liquid-cooled systems.
- Air-cooled systems: In air-cooled systems, the generator is cooled by drawing in cool air through the ventilation system and forcing it over the generator’s components. The air-cooled system comprises a fan, air ducts, and a heat exchanger or radiator. The fan draws in cool air through the ventilation system and forces it over the generator’s components, while the heat exchanger or radiator removes the heat absorbed from the generator and dissipates it to the surrounding environment.
- Liquid-cooled systems: In liquid-cooled systems, a coolant, typically water or a mixture of water and coolant, circulates through the engine block and absorbs heat from the generator. The coolant is then transferred to a radiator, where the heat is dissipated to the surrounding environment. The liquid-cooled system comprises a pump, radiator, coolant, and filters. The pump circulates the coolant through the engine block and radiator, while the radiator removes the heat absorbed by the coolant. The coolant and oil filters remove debris and contaminants from the coolant and oil, respectively, to maintain the efficiency of the cooling system.
The functions of cooling systems in electric generators are to remove heat from the generator, maintain a safe operating temperature, and prevent damage to the generator’s components. Proper maintenance and regular inspection of cooling systems are crucial to ensure efficient and safe operation of electric generators.
Types Of Cooling Systems (Air-Cooled And Liquid-Cooled)
Electric generators use two main types of cooling systems: air-cooled and liquid-cooled.
- Air-cooled systems: In an air-cooled system, the generator is cooled by drawing in air through the ventilation system and forcing it over the generator’s components. The air-cooled system typically includes a fan, air ducts, and a heat exchanger or radiator. The fan draws in cool air through the ventilation system and forces it over the generator’s components, while the heat exchanger or radiator removes the heat absorbed from the generator and dissipates it to the surrounding environment.
Air-cooled systems are typically simpler and less expensive to maintain than liquid-cooled systems. They are also generally more compact and lighter in weight, making them a suitable choice for portable generators.
- Liquid-cooled systems: In a liquid-cooled system, a coolant, usually a mixture of water and antifreeze, circulates through the engine block and absorbs heat from the generator. The coolant is then transferred to a radiator, where the heat is dissipated to the surrounding environment. The liquid-cooled system typically includes a pump, radiator, coolant, and filters. The pump circulates the coolant through the engine block and radiator, while the radiator removes the heat absorbed by the coolant. The coolant and oil filters remove debris and contaminants from the coolant and oil, respectively, to maintain the efficiency of the cooling system.
Liquid-cooled systems are typically more efficient and effective in removing heat from the generator than air-cooled systems. They are also suitable for larger generators that require a higher capacity for heat dissipation. However, they are typically more expensive and require more maintenance than air-cooled systems.
In summary, both air-cooled and liquid-cooled systems have their advantages and disadvantages, and the choice between the two depends on factors such as generator size, application, and budget.
Components Of Air-Cooled And Liquid-Cooled Systems
The components of air-cooled and liquid-cooled systems in electric generators differ due to their different methods of cooling.
Components of Air-Cooled Systems:
- Fan: The fan is responsible for drawing in cool air through the ventilation system and forcing it over the generator’s components.
- Air Ducts: The air ducts direct the airflow over the generator’s components and channel the hot air out of the generator.
- Heat Exchanger/Radiator: The heat exchanger or radiator removes the heat absorbed from the generator and dissipates it to the surrounding environment.
Components of Liquid-Cooled Systems:
- Coolant: The coolant, usually a mixture of water and antifreeze, is circulated through the engine block to absorb heat from the generator.
- Radiator: The radiator removes the heat absorbed by the coolant and dissipates it to the surrounding environment.
- Water Pump: The water pump circulates the coolant through the engine block and radiator.
- Thermostat: The thermostat regulates the coolant temperature to ensure that the generator is operating at an optimal temperature.
- Filters: The coolant and oil filters remove debris and contaminants from the coolant and oil, respectively, to maintain the efficiency of the cooling system.
In addition to these components, both air-cooled and liquid-cooled systems may also have cooling fins, which increase the surface area of the generator to facilitate heat dissipation.
Overall, the components of cooling systems are essential for maintaining safe operating temperatures in electric generators and preventing damage to the generator’s components. Proper maintenance and regular inspection of these components are necessary to ensure the efficient and safe operation of electric generators.
Maintenance And Troubleshooting
Regular maintenance and troubleshooting are essential for ensuring the efficient and safe operation of electric generators.
Maintenance:
- Air filters: The air filter should be cleaned or replaced regularly to ensure that the airflow is not obstructed and that the generator is receiving sufficient air for cooling.
- Oil and coolant levels: The oil and coolant levels should be checked regularly and topped off if necessary.
- Cooling system components: The cooling system components should be inspected regularly for signs of damage or wear, such as leaks, cracks, or corrosion.
- Fan blades: The fan blades should be inspected for damage and cleaned regularly to ensure that the airflow is not obstructed.
- Radiator: The radiator should be cleaned regularly to prevent the accumulation of dirt, debris, or other materials that can reduce the efficiency of the cooling system.
Troubleshooting:
- Overheating: If the generator is overheating, it may be due to a clogged air filter, low coolant level, or malfunctioning cooling system components. The generator should be shut down immediately and the cooling system inspected for the cause of the overheating.
- Low coolant level: If the coolant level is low, it may be due to a leak in the cooling system or a faulty water pump. The generator should be shut down immediately and the cooling system inspected for leaks or other issues.
- Malfunctioning fan: If the fan is not working properly, it may be due to a broken fan blade, faulty motor, or malfunctioning thermostat. The generator should be shut down immediately and the cooling system inspected for the cause of the malfunctioning fan.
In summary, regular maintenance and troubleshooting are essential for ensuring the efficient and safe operation of electric generators. Proper maintenance can prevent issues from arising, while troubleshooting can help identify and resolve any problems that may arise.
Importance Of Regular Maintenance
Regular maintenance is crucial for ensuring the efficient and safe operation of electric generators. Here are some reasons why:
- Prevents breakdowns and downtime: Regular maintenance can prevent breakdowns and minimize downtime, which is essential for businesses and industries that rely on electric generators for their operations. By identifying and resolving issues early on, maintenance can prevent more significant problems from occurring, leading to costly downtime.
- Extends the lifespan of the generator: Regular maintenance can also extend the lifespan of the generator, as it can prevent premature wear and tear on the generator’s components. Over time, this can save businesses and industries money by avoiding the need to replace the generator earlier than expected.
- Ensures safety: Electric generators can be dangerous if not properly maintained, as they can overheat or even catch fire. Regular maintenance can prevent these hazards from occurring and ensure the safety of the generator’s operators and the surrounding environment.
- Maintains efficiency: Proper maintenance can help maintain the efficiency of the generator, ensuring that it is operating at optimal levels. This can lead to savings in fuel consumption and electricity costs, as the generator is not working harder than it needs to.
- Compliance with regulations: Regular maintenance is often required to comply with regulatory standards and guidelines, ensuring that businesses and industries are operating safely and responsibly.
In summary, regular maintenance is crucial for ensuring the efficient and safe operation of electric generators. It can prevent breakdowns and downtime, extend the generator’s lifespan, ensure safety, maintain efficiency, and comply with regulatory standards.
Common Issues Related To Air Circulation In Electric Generators
There are several common issues related to air circulation in electric generators that can lead to reduced performance, overheating, and even complete failure of the generator. Here are some of the most common issues:
- Clogged air filter: A clogged air filter can restrict the flow of air to the generator’s cooling system, leading to reduced cooling efficiency and potential overheating. Over time, the clogged filter can also cause damage to other parts of the generator.
- Obstructed airflow: Any obstruction in the airflow path, such as debris or dust, can reduce the cooling efficiency of the generator. This can lead to overheating and even complete failure of the generator.
- Low coolant level: If the coolant level is low, the generator may not be able to effectively cool the engine, leading to overheating and potential damage to the generator’s components.
- Malfunctioning fan: If the fan is not working properly, it may not be able to effectively circulate air through the cooling system, leading to reduced cooling efficiency and potential overheating.
- Damaged radiator: If the radiator is damaged or corroded, it may not be able to effectively transfer heat away from the engine, leading to reduced cooling efficiency and potential overheating.
- Inadequate ventilation: If the generator is installed in an area with inadequate ventilation, it may not be able to effectively dissipate heat, leading to potential overheating and damage to the generator’s components.
In summary, common issues related to air circulation in electric generators include clogged air filters, obstructed airflow, low coolant levels, malfunctioning fans, damaged radiators, and inadequate ventilation. It is important to regularly inspect and maintain the generator’s cooling system to prevent these issues from occurring.
Troubleshooting Tips For Air Circulation Problems
If you are experiencing air circulation problems with your electric generator, here are some troubleshooting tips that may help:
- Check the air filter: If the air filter is clogged, clean or replace it. This will help to ensure that air can flow freely through the generator’s cooling system.
- Check for obstructions: Look for any debris or dust that may be obstructing the airflow path. Remove any obstructions to improve the cooling efficiency of the generator.
- Check the coolant level: Make sure the coolant level is at the appropriate level. If it is low, add more coolant as needed to ensure the generator can effectively cool the engine.
- Check the fan: Inspect the fan to ensure it is working properly. If it is not, repair or replace it to improve the cooling efficiency of the generator.
- Check the radiator: Inspect the radiator for damage or corrosion. If it is damaged, repair or replace it to ensure effective heat transfer away from the engine.
- Check the ventilation: Make sure the generator is installed in an area with adequate ventilation. If necessary, install additional ventilation to ensure that heat can be dissipated effectively.
- Consider upgrading the cooling system: If the above steps do not resolve the air circulation problems, consider upgrading the cooling system to a more efficient one. A professional can help with this.
In summary, troubleshooting air circulation problems in electric generators involves checking and cleaning the air filter, removing obstructions, checking the coolant level, inspecting and repairing the fan and radiator, ensuring adequate ventilation, and considering upgrading the cooling system if necessary.
Frequently Asked Questions (FAQs) Why Electric Generators Need Proper Air Circulation
Why do electric generators need proper air circulation?
Electric generators need proper air circulation to dissipate the heat generated during operation. Without proper air circulation, the generator can overheat and potentially cause damage to its components or even fail completely.
What happens if an electric generator overheats?
If an electric generator overheats, it can cause damage to its components, including the engine, and potentially even result in a fire. Regular maintenance and proper air circulation are important to prevent overheating.
How do air-cooled and liquid-cooled cooling systems differ?
Air-cooled cooling systems rely on air to dissipate heat from the generator, while liquid-cooled systems use a liquid, typically water, to transfer heat away from the generator’s components.
What are some common issues related to air circulation in electric generators?
Common issues related to air circulation in electric generators include clogged air filters, obstructed airflow, low coolant levels, malfunctioning fans, damaged radiators, and inadequate ventilation.
How can air circulation problems in electric generators be troubleshot?
To troubleshoot air circulation problems in electric generators, check the air filter, look for obstructions, check the coolant level, inspect and repair the fan and radiator, ensure adequate ventilation, and consider upgrading the cooling system if necessary. Regular maintenance is also important to prevent air circulation problems from occurring.
Conclusion
In conclusion, proper air circulation is essential for the efficient and safe operation of electric generators. Without adequate air circulation, generators can overheat and potentially cause damage to their components or even fail completely. Regular maintenance and proper installation are important to prevent air circulation problems and ensure the longevity and reliability of the generator.
If you experience air circulation problems, it is important to troubleshoot the issue promptly and effectively to prevent further damage. By following proper maintenance and troubleshooting procedures, you can ensure that your generator operates safely and efficiently for years to come.